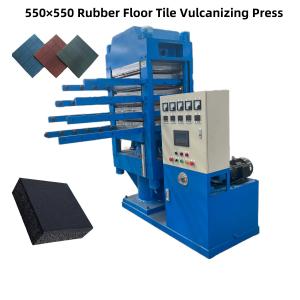
Qingdao Beishun Environmental Protection Technology Co.,Ltd
Companies adhere to the "first-class quality to gain market confidence, quality service to win customer satisfaction, continuous improvement of enterprise development seek to establish a corporate
Add to Cart
PLC Automatic Control 4-Layer Rubber Floor Tile Vulcanizing Machine / Rubber Granule Floor Tile Making Machine
Floor tile vulcanizing machine introduction:
The working principle of the rubber floor tile vulcanizer is to heat, pressurize and vulcanize the raw materials of the rubber floor tiles to undergo physical and chemical changes under high temperature and high pressure to form them. The specific process includes the following steps:
1. Heating and pressurizing: The rubber floor tile vulcanizer heats and pressurizes the rubber material through the electric heating plate. The electric heating plate can be controlled separately to ensure the accuracy of temperature control
2. Vulcanization treatment: Under high temperature and high pressure, the rubber material undergoes a cross-linking reaction to form a stable three-dimensional network structure. This process significantly improves the strength, wear resistance and anti-aging properties of rubber.
3. Technical parameters of rubber floor tile vulcanizer include:
Nominal clamping force: such as 110 tons or 160 tons
Hot plate specifications: such as 1100x1100mm
Hot plate spacing: such as 500mm or 300mm
Plunger stroke: such as 700mm or 300mm
Plunger diameter: such as 320mm or 360mm
Motor power: such as 5.5KW
Hot plate unit area pressure: such as 12kg/cm²
Weight: about 7000kg
4. Structural mode: such as four-column or frame type
The application scenario of rubber floor tile vulcanizer is mainly in the production process of rubber floor tiles, through heating, pressurizing and vulcanizing the rubber material, to produce floor tile products with good physical and chemical properties. This equipment is widely used in various production lines that require high-quality rubber products.
Technical parameter:
Model | XLB-D 550*550*4 | XLB-D 1200*1200*2 |
Total Pressure | 50T | 200T |
Hot plate size | 550*550*60mm | 1200*1200*80mm |
Plate spacing | 150mm | 200mm |
Working layer | 4 | 2 |
Hot plate quantity | 5 | 3 |
Piston stoke | 400mm | 400mm |
Piston quantity | 1 set | 1 set |
Piston diameter | 200mm | 360mm |
Structure | Four columns | Frame |
Max. heating temperature | Electricity Mode 250ºC | Electricity Mode 250ºC |
Motor power | 2.2kw | 2.2kw |
Dimension | 2200*900*2200mm | 2500*960*2500mm |
Weight | 3600kg | 8300kg |
Basic structure and use of flat vulcanizer
First, briefly introduce the flat vulcanizer, then disassemble its basic structure in detail, including the functions and working principles of each part, and finally explain its use in different industries, so that you can fully understand the flat vulcanizer.
Today, I will talk about this magical equipment, the flat vulcanizer! In the field of industrial production, it has a very important position.
1. Frame part.
Structure: The frame is the basic support part of the flat vulcanizer, usually composed of left and right columns, upper beams and lower beams connected by bolts or welding to form a stable frame structure. The columns are generally made of high-quality steel and have sufficient strength and rigidity to withstand the huge pressure generated during the vulcanization process. The upper and lower beams are relatively wide and thick, and are used to install the heating plate and related transmission and control components.
Function: The main function of the frame is to provide stable support for the entire flat vulcanizer, to ensure that the relative positions of the components are fixed during the vulcanization process, thereby ensuring the accuracy and stability of the vulcanization process. For example, when vulcanizing large rubber products, the rack needs to be able to withstand several tons or even tens of tons of pressure. If the rack is not stable enough, the plate will be displaced, affecting the product quality.
2. Heating system.
Structure: The heating system is mainly composed of a heating plate, a heating medium circulation device and a temperature control system. The heating plate is generally a multi-layer structure with a heating channel inside, which can be heated by steam, thermal oil or electric heating elements. Taking electric heating as an example, resistance wires are evenly distributed in the heating plate, and heat is generated by passing current through the resistance wires, thereby increasing the temperature of the plate. The heating medium circulation device is used to circulate the heating medium (such as thermal oil) in the channel of the heating plate to ensure that the temperature of the plate is uniform. The temperature control system consists of a temperature sensor, a temperature control instrument, etc. The temperature sensor monitors the temperature of the heating plate in real time and transmits the signal to the temperature control instrument. The temperature control instrument controls the working state of the heating element according to the set temperature value to achieve precise temperature control.
3.Function: The core function of the heating system is to provide a suitable temperature environment for the vulcanization process. The vulcanization reaction of rubber needs to be carried out smoothly within a certain temperature range. Different rubber formulas and products require different vulcanization temperatures. For example, the vulcanization temperature of ordinary rubber tires is about 140℃-180℃, while some special rubbers may require higher temperatures. Accurate temperature control can ensure uniform vulcanization of rubber products, improve product quality, and avoid the problem of under-vulcanization or over-vulcanization of products due to too high or too low temperature.